Découvrez comment le pilotage des charges industrielles en fonction de la production solaire réduit vos factures, sécurise votre approvisionnement et améliore votre bilan carbone. Guide détaillé : stratégies, technologies, ROI et études de cas.
Dans un contexte économique marqué par une volatilité croissante des prix de l’énergie et une pression réglementaire accrue (décret tertiaire, objectifs de réduction des émissions de CO2), l’industrie française et européenne fait face à un défi majeur : maintenir sa compétitivité tout en réduisant son impact environnemental.
Le photovoltaïque (PV) apparaît comme une réponse pertinente, offrant une source d’énergie locale, décarbonée et de plus en plus compétitive pour les sites industriels. Cependant, un obstacle majeur persiste : la variabilité intrinsèque de la production solaire, qui contraste avec les besoins souvent constants ou spécifiques des processus industriels. Cette inadéquation peut entraîner soit une injection coûteuse d’électricité dans le réseau, soit un soutirage au réseau à des moments économiquement défavorables.
C’est ici qu’intervient le pilotage intelligent des charges industrielles : une approche stratégique visant à synchroniser la demande énergétique avec la production solaire locale. Cette méthode transforme une contrainte apparente en opportunité d’optimisation et de réduction des coûts.
Dans cet article, nous explorerons en profondeur pourquoi et comment mettre en œuvre un pilotage efficace des charges industrielles en fonction de la production solaire, les technologies disponibles, ainsi que des exemples concrets d’application et les résultats obtenus.
Pourquoi le Pilotage des Charges est Crucial en Contexte Industriel ?
Les Avantages Spécifiques pour l’Industrie
Réduction Drastique des Coûts Énergétiques
Le pilotage des charges en fonction de la production solaire permet de maximiser l’autoconsommation, un facteur économique déterminant. Deux indicateurs clés doivent être distingués :
- Le taux d’autoconsommation : proportion de l’énergie solaire produite qui est effectivement consommée sur site
- Le taux d’autoproduction : part de la consommation totale couverte par la production solaire locale
Un pilotage intelligent permet généralement d’augmenter le taux d’autoconsommation de 50-60% à 80-90%, selon la nature des charges disponibles. Cette optimisation se traduit directement par des économies substantielles, avec un retour sur investissement (ROI) typiquement compris entre 3 et 7 ans pour l’ensemble du système (installation PV + système de pilotage).
Le pilotage permet également d’éviter les pics de consommation et les tarifs aux heures pleines/pointe, période où le coût de l’électricité peut être multiplié par 5. Pour une installation industrielle moyenne consommant 2 GWh/an, cela peut représenter une économie annuelle de 50 000 à 120 000 euros.
Enfin, la flexibilité ainsi créée peut être valorisée sur les marchés de l’énergie via les mécanismes d’effacement, générant des revenus complémentaires potentiels de 5 000 à 25 000 euros par MW de capacité effaçable.
Sécurité et Résilience Énergétique
Le pilotage des charges en fonction de la production solaire réduit significativement la dépendance au réseau et à ses fluctuations, tant en termes de prix que de disponibilité. Cette autonomie partielle constitue un avantage stratégique dans un contexte d’incertitude énergétique.
En cas de limitations réseau ou d’événements externes (tension sur le réseau électrique, délestage), un système bien configuré permet de maintenir les fonctions critiques opérationnelles, assurant ainsi la continuité des opérations essentielles. Cette résilience accrue représente une valeur ajoutée considérable, bien que difficilement quantifiable en termes purement financiers.
Atteinte des Objectifs RSE et Réglementaires
La réduction de l’empreinte carbone est un bénéfice majeur de cette approche. Pour chaque kWh d’électricité solaire autoconsommé, c’est environ 60g de CO2 économisés par rapport au mix électrique français, et jusqu’à 400g dans certains pays européens à mix plus carboné.
Cette démarche contribue directement à la conformité avec les exigences réglementaires croissantes, notamment le Décret Tertiaire qui impose une réduction progressive de la consommation énergétique des bâtiments tertiaires, y compris industriels. Le pilotage intelligent est reconnu comme une action significative dans ce cadre.
L’impact positif sur l’image de marque ne doit pas être négligé : les entreprises engagées dans l’optimisation énergétique améliorent leur réputation auprès des clients, partenaires et investisseurs de plus en plus sensibles aux questions environnementales.
Optimisation des Process Industriels
Pour certains procédés non-critiques, le pilotage énergétique permet d’établir un lien vertueux entre disponibilité énergétique et planification de production. Par exemple, certaines opérations énergivores comme le broyage, la compression d’air ou le prétraitement de matériaux peuvent être programmées pendant les périodes de forte production solaire, optimisant ainsi l’ensemble du processus industriel.
Comprendre les Composantes Clés
La Production Solaire en Milieu Industriel
Les sites industriels offrent généralement d’excellentes opportunités pour l’installation de panneaux photovoltaïques, avec trois principales configurations :
- Installations en toiture : valorisation des grandes surfaces de toit, généralement entre 500 kWc et 3 MWc selon la superficie disponible
- Ombrières de parking : double fonction de production d’électricité et d’abri pour les véhicules
- Installations au sol : pour les sites disposant d’espaces non utilisés, permettant des puissances plus importantes
Les profils de production solaire suivent des cycles prévisibles mais variables, avec des pics en milieu de journée et une production maximale en été. Cette production est influencée par plusieurs facteurs :
- Météorologie (ensoleillement, nébulosité)
- Saisonnalité
- Orientation et inclinaison des panneaux
- Température (le rendement diminuant lorsque la température des panneaux augmente)
La prévision de production solaire constitue un élément fondamental de tout système de pilotage. Les technologies actuelles permettent d’obtenir des prévisions avec une précision de 85-95% à J+1, en intégrant des données météorologiques locales et des modèles prédictifs sophistiqués.
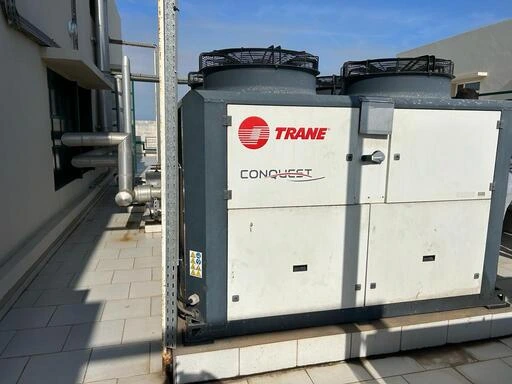
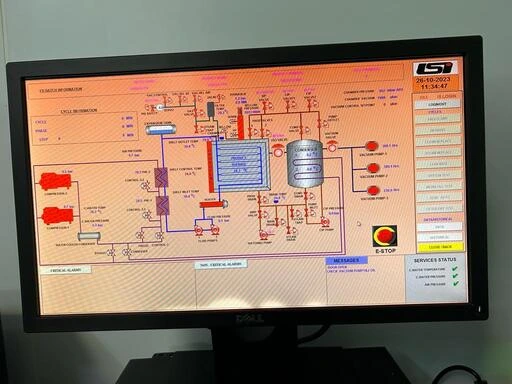
Les Charges Industrielles : Un Défi Spécifique
Caractéristiques des Charges Industrielles
Les sites industriels se caractérisent par des consommations électriques présentant plusieurs spécificités :
- Forte puissance : moteurs industriels (20 kW à plusieurs MW), fours (50 kW à plusieurs MW), systèmes CVC lourds (30-500 kW), compresseurs (15-200 kW)
- Profils variés : certaines charges sont constantes (fours maintenus à température), d’autres cycliques (compresseurs, pompes) ou variables (lignes de production)
- Criticité différenciée : certains équipements ne peuvent jamais être arrêtés ou modulés sans impact sur la production ou la sécurité
Ces caractéristiques créent à la fois des défis et des opportunités pour le pilotage en fonction de la production solaire.
Identification des Charges Pilotables (Flexibles)
L’identification précise des charges pilotables constitue une étape cruciale. On distingue trois catégories principales :
- Charges décalables : peuvent être déplacées dans le temps sans impact majeur
- Chauffage/refroidissement de locaux ou de process non critiques
- Recharge de flottes de véhicules électriques
- Systèmes de pompage avec stockage
- Certains batchs de production planifiables
- Charges modulables : peuvent fonctionner à puissance variable
- Équipements avec variation de vitesse (pompes, ventilateurs)
- Systèmes thermiques avec plages de température acceptables
- Certains process industriels avec paramètres ajustables
- Charges effaçables : peuvent être temporairement arrêtées
- Équipements avec inertie thermique importante
- Processus interruptibles sans impact sur la qualité
- Systèmes redondants
Un audit énergétique approfondi est nécessaire pour identifier ces potentiels. La méthodologie recommandée comprend :
- Installation de sous-compteurs par poste de consommation
- Analyse des courbes de charge sur plusieurs semaines/mois
- Entretiens avec les responsables de production et maintenance
- Analyse des contraintes techniques et opérationnelles
- Tests ponctuels de modulation pour vérifier l’absence d’impact
Les Systèmes de Pilotage des charges (EMS – Energy Management System)
L’Energy Management System (EMS) constitue le cerveau de l’installation. Un EMS industriel adapté au pilotage solaire comprend typiquement :
- Capteurs et compteurs : mesure en temps réel de la production solaire et des consommations par poste
- Automates programmables (API/PLC) : contrôle direct des équipements pilotables
- Logiciel de supervision et d’optimisation (SCADA) : centralisation des données, algorithmes d’optimisation, interface utilisateur
- Interfaces de communication : protocoles permettant le dialogue entre les différents composants
Ces systèmes doivent répondre aux exigences industrielles de fiabilité, sécurité et redondance, tout en offrant la flexibilité nécessaire à l’optimisation énergétique.
Stratégies et Technologies de Pilotage des charges
Stratégies de Pilotage Adaptées à l’Industrie
Maximisation de l’Autoconsommation Directe
La priorisation des charges pendant les heures de production solaire constitue la stratégie de base. Elle consiste à :
- Identifier les charges les plus énergivores et flexibles
- Programmer leur fonctionnement pendant les périodes de forte production solaire
- Implémenter des algorithmes de Load Shifting (décalage temporel) qui déplacent automatiquement certaines consommations en fonction des prévisions de production
Cette approche permet typiquement d’augmenter le taux d’autoconsommation de 20 à 30 points de pourcentage.
Lissage de la Courbe de Charge
L’écrêtage des pointes (Peak Shaving) vise à maintenir la puissance soutirée sous un seuil défini, réduisant ainsi les coûts liés à la puissance souscrite et aux dépassements. Deux approches complémentaires sont possibles :
- Pilotage direct des charges : réduction temporaire de la puissance de certains consommateurs
- Utilisation de batteries : décharge pendant les pics de consommation
Pour un site industriel moyen, cette stratégie peut permettre de réduire la puissance souscrite de 10-30%, représentant une économie annuelle de plusieurs milliers d’euros.
Pilotage des charges Prédictif Basé sur la Météo et les Plans de Production
Les systèmes avancés intègrent :
- Prévisions météorologiques locales à 24-72h
- Plannings de production industrielle
- Algorithmes d’optimisation qui ajustent dynamiquement le pilotage
Les technologies d’Intelligence Artificielle et de Machine Learning permettent d’affiner continuellement les prévisions et d’optimiser les décisions, avec des gains d’efficacité supplémentaires de 5-15% par rapport aux systèmes conventionnels.
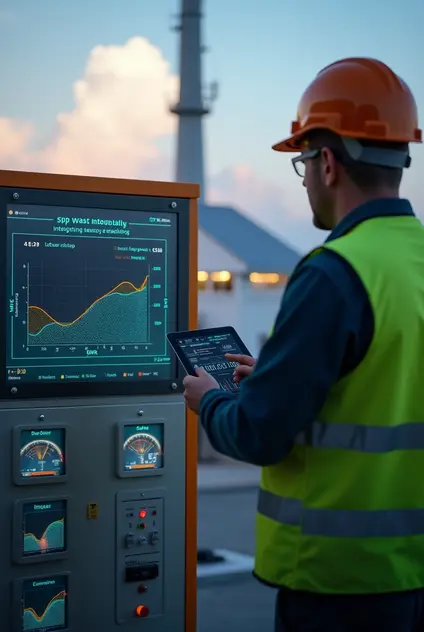
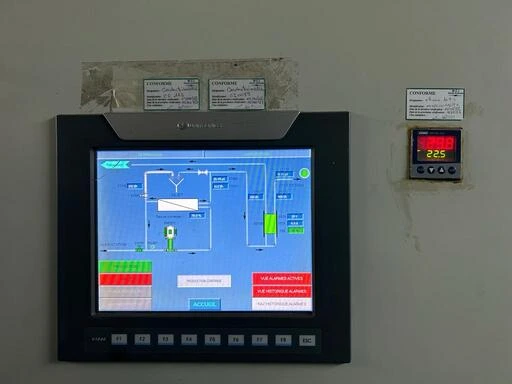
Intégration du Stockage (Batteries et pilotage des charges)
Le stockage par batteries représente un complément idéal au pilotage des charges, permettant de :
- Stocker le surplus solaire pour une utilisation différée
- Lisser la courbe de charge
- Réaliser de l’arbitrage énergétique (stockage aux heures creuses, décharge aux heures pleines)
Si les coûts restent significatifs (300-600€/kWh installé en 2024), la rentabilité peut être atteinte dans certains contextes industriels, particulièrement lorsque le différentiel de prix entre heures creuses et pleines est important.
Participation à la Flexibilité Réseau
Les installations industrielles peuvent valoriser leur flexibilité sur différents marchés :
- Services système (réglage de fréquence)
- Mécanisme de capacité
- Effacement rémunéré sur les marchés de gros ou via des agrégateurs
Cette participation peut générer des revenus complémentaires significatifs tout en contribuant à la stabilité du réseau électrique.
Technologies et Protocoles de Communication
L’interopérabilité constitue un enjeu majeur pour le pilotage énergétique industriel. Les protocoles les plus couramment utilisés sont :
- Modbus : standard industriel robuste et largement déployé
- Profinet : protocole temps réel, particulièrement répandu dans l’industrie allemande
- OPC UA : standard ouvert offrant sécurité et interopérabilité avancées
La cybersécurité représente une préoccupation croissante, les systèmes énergétiques devenant des cibles potentielles. Des solutions certifiées avec chiffrement, authentification forte et surveillance continue sont désormais indispensables.
Les solutions disponibles sur le marché comprennent :
- Systèmes EMS complets : plateformes intégrées de gestion énergétique avec modules spécifiques pour le solaire
- Contrôleurs dédiés : équipements spécialisés pour le pilotage de charges spécifiques
- Logiciels d’optimisation : solutions analytiques avancées intégrables aux infrastructures existantes
- Services cloud : plateformes SaaS offrant analyses et optimisation à distance
Mise en Œuvre Pratique : Étapes Clés et Bonnes Pratiques
Guide Pas-à-Pas pour l’Industriel (pilotage des charges)
Étape 1 : Audit Énergétique Approfondi & Analyse de Flexibilité
Cette phase initiale critique comprend :
- Cartographie détaillée des consommations (sous-comptage par poste)
- Analyse des courbes de charge historiques
- Évaluation du potentiel solaire du site (surfaces disponibles, orientation, ombrage)
- Identification des charges pilotables et de leur degré de flexibilité
- Simulation des économies potentielles et dimensionnement préliminaire
Durée typique : 1-3 mois, selon la complexité du site.
Étape 2 : Définition des Objectifs & Stratégie
Cette phase stratégique détermine :
- Objectifs chiffrés (taux d’autoconsommation visé, économies annuelle cibles, etc.)
- Niveau de complexité acceptable du système
- Degré d’autonomie souhaité vs. nécessité d’intervention humaine
- Budget d’investissement et ROI attendu
- Calendrier de déploiement
Étape 3 : Conception du Système
La conception détaillée inclut :
- Dimensionnement précis de l’installation PV
- Architecture technique de l’EMS
- Spécification des interfaces avec les systèmes existants
- Définition des algorithmes de pilotage
- Plan de déploiement et de mise en service
Étape 4 : Sélection des Fournisseurs et Technologies
Cette étape critique implique :
- Rédaction d’un cahier des charges précis
- Consultation d’intégrateurs spécialisés
- Analyse comparative des offres (prix, performances, références)
- Vérification de la compatibilité avec l’infrastructure existante
- Négociation des conditions contractuelles et garanties de performance
Étape 5 : Installation, Intégration & Commissioning
Le déploiement représente souvent la phase la plus délicate, comprenant :
- Installation physique des équipements (panneaux, compteurs, contrôleurs)
- Raccordement électrique et communication
- Configuration des logiciels et algorithmes
- Tests d’intégration avec les systèmes existants
- Phase de commissioning avec vérification des performances
L’intégration avec les process industriels existants constitue un point critique nécessitant une planification minutieuse pour minimiser les perturbations opérationnelles.
Étape 6 : Monitoring, Maintenance & Optimisation Continue
La phase d’exploitation implique :
- Suivi continu des performances (production, consommation, taux d’autoconsommation)
- Maintenance préventive des équipements
- Ajustements réguliers des algorithmes d’optimisation
- Formation continue des équipes
- Rapports périodiques d’analyse et recommandations d’amélioration
Points de Vigilance et Facteurs de Succès
Plusieurs facteurs déterminent la réussite d’un projet de pilotage des charges :
- Implication des équipes opérationnelles : la maintenance et la production doivent être parties prenantes dès le début du projet
- Qualité des données de mesure : des capteurs précis et fiables sont indispensables à l’optimisation
- Sécurité des systèmes : tant opérationnelle (redondances, modes dégradés) que cyber (protection contre les intrusions)
- Choix d’un intégrateur compétent : l’expertise spécifique en milieu industriel est déterminante
- Connaissance du cadre réglementaire : notamment les conditions d’injection-revente, d’autoconsommation collective et les aides financières disponibles (CEE, appels à projets ADEME, subventions régionales)
Études de Cas et Exemples Concrets
Retours d’Expérience d’Industriels
Cas 1 : Site Agroalimentaire (pilotage des charges)
Secteur d’activité : Production de produits laitiers Problématique initiale : Facture électrique annuelle de 450 000€ avec forte consommation pour la réfrigération et le chauffage de process
Solution mise en place :
- Installation PV en toiture de 750 kWc
- Pilotage intelligent des groupes froids et des tanks de chauffage
- Stockage thermique (eau glacée et eau chaude) comme tampon énergétique
- EMS avec prévision de production à 72h et intégration au planning de production
Résultats obtenus :
- Taux d’autoconsommation : 87%
- Économies annuelles : 112 000€
- Réduction des émissions CO2 : 85 tonnes/an
- ROI global : 5,3 ans (avec aides)
- Bénéfice qualitatif : meilleure planification de la production
Cas 2 : Usine Métallurgique (pilotage des charges)
Secteur d’activité : Transformation de métaux non ferreux Problématique initiale : Consommation électrique très intense mais avec certains process flexibles
Solution mise en place :
- Installation PV au sol de 1,8 MWc
- Pilotage des fours électriques non critiques
- Modulation de la puissance des compresseurs d’air
- Intégration du système de pilotage aux automates existants
- EMS avec priorisation automatique des charges
Résultats obtenus :
- Taux d’autoconsommation : 93%
- Économies annuelles : 225 000€
- Réduction de la puissance souscrite : 18%
- Réduction des émissions CO2 : 210 tonnes/an
- ROI global : 6,1 ans
- Valorisation de la flexibilité : 15 000€/an de revenus complémentaires
Cas 3 : Centre Logistique Réfrigéré (pilotage des charges)
Secteur d’activité : Logistique alimentaire sous température dirigée Problématique initiale : Consommation importante pour la réfrigération, besoin de sécurisation énergétique
Solution mise en place :
- Installation PV en toiture et ombrières (1,2 MWc)
- Pilotage prédictif des groupes froids avec prérefroidissement anticipatif
- Stockage par batteries (250 kWh) pour lissage et sécurité
- EMS avec IA pour optimisation continue
Résultats obtenus :
- Taux d’autoconsommation : 78%
- Économies annuelles : 168 000€
- Autonomie partielle en cas de coupure réseau : 4-6h pour les équipements critiques
- Réduction des émissions CO2 : 140 tonnes/an
- ROI global : 7,2 ans (inclusion du stockage)
- Bénéfice qualitatif : résilience accrue, valorisation marketing
FAQ : Vos Questions sur le Pilotage des Charges Industrielles
Q1 : Quelles sont les charges industrielles les plus facilement pilotables ? Les systèmes de chauffage et refroidissement avec inertie thermique (HVAC, froid industriel), les systèmes de pompage avec stockage, la compression d’air avec réservoirs tampons et les processus de charge (batteries, véhicules électriques) sont généralement les plus adaptés au pilotage.
Q2 : Quelle puissance photovoltaïque installer pour un site industriel ? Le dimensionnement optimal dépend de plusieurs facteurs : consommation de base, superficie disponible, budget et objectifs d’autoconsommation. En règle générale, une installation couvrant 20-40% de la consommation annuelle offre le meilleur compromis entre investissement et rentabilité.
Q3 : Le stockage par batteries est-il rentable en contexte industriel ? La rentabilité du stockage dépend fortement du profil de consommation et des tarifs d’électricité. En 2024, les batteries deviennent économiquement viables dans les contextes de fort différentiel tarifaire (>0,10€/kWh entre heures creuses et pleines) ou lorsque la sécurisation énergétique représente un enjeu critique.
Q4 : Comment évaluer le potentiel d’économies pour mon site ? Un audit énergétique spécialisé est nécessaire, mais une estimation préliminaire peut être réalisée en analysant les factures électriques des 12 derniers mois, les courbes de charge journalières et le potentiel solaire local. Le taux d’économie typique se situe entre 15% et 35% de la facture totale.
Q5 : Quels sont les aides financières disponibles pour ces projets ? Plusieurs dispositifs sont mobilisables : Certificats d’Économie d’Énergie (CEE), appels à projets ADEME, aides régionales à la décarbonation, amortissements accélérés et prêts à taux bonifiés. Ces aides peuvent couvrir 15% à 40% du coût total du projet selon sa nature et sa localisation.
Tendances Futures et Conclusion
L’Avenir du Pilotage des charges Énergétique Industriel
Le domaine du pilotage énergétique industriel évolue rapidement, avec plusieurs tendances prometteuses :
L’Intelligence Artificielle et les jumeaux numériques transforment l’optimisation énergétique, permettant une précision accrue dans les prévisions et une adaptation dynamique en temps réel. Les systèmes auto-apprenants peuvent améliorer leurs performances de 3-5% chaque année.
L’intégration aux Communautés d’Énergie Renouvelable (CER) ou aux Centrales Virtuelles (VPP) ouvre de nouvelles perspectives. Les sites industriels peuvent ainsi participer à des écosystèmes énergétiques locaux, maximisant l’utilisation des ressources renouvelables à l’échelle d’une zone d’activité ou d’un territoire.
Le pilotage multi-énergies (électricité, gaz, chaleur) représente la prochaine frontière, avec une optimisation globale des flux énergétiques et la valorisation des synergies intersectorielles.
L’évolution de la réglementation et des marchés de l’énergie, notamment avec la tarification dynamique et la valorisation croissante de la flexibilité, renforcera encore l’intérêt économique du pilotage intelligent.
Conclusion : Passez à l’Action
Le pilotage des charges industrielles en fonction de la production solaire constitue désormais un levier stratégique pour l’industrie, alliant performance économique et environnementale. Les bénéfices sont multiples et substantiels :
- Réduction significative des coûts énergétiques
- Amélioration de la résilience et de l’autonomie énergétique
- Contribution concrète aux objectifs environnementaux
- Valorisation possible de la flexibilité
Face aux défis énergétiques actuels, cette approche représente une réponse pragmatique et efficace, avec un retour sur investissement généralement compris entre 3 et 7 ans.
N’attendez plus pour explorer le potentiel de cette solution pour votre site industriel. Contactez nos experts pour un pré-diagnostic gratuit et découvrez comment optimiser votre consommation énergétique tout en réduisant votre empreinte carbone.